News
How is water jet cutting machine cut?
28/6/2022
Junda Water jet cutting machine is water jet cutting, commonly known as water knife. With the development of science and technology, this cold cutting method will be applied to more fields. Here is a brief introduction to what water cutting is.
water jet cutting principle
Water jet cutting is a new cold machining technology. Can be used in bad conditions, prohibited fireworks, widely concerned. Water jet cutting is a combination of machinery, electronics and computers. The high-tech achievements of the whole automatic control technology is a new material processing method developed in recent years.
The principle of water jet cutting is to use a certain high pressure pure water or slurry with cutting abrasive, through the cutting nozzle injection liquid column with high density impact force, directly impact to be processed for cutting. According to the different water pressure, it can be divided into low pressure water jet cutting and high pressure water jet cutting.
water jet cutting characteristics
Water jet cutting technology has the following characteristics:
(1) Cutting water jet pressure is large. The pressure of the water jet is tens to hundreds of megapascals, which is 2 to 3 times the speed of sound, creating a huge energy density of the jet to cut objects. The cutting temperature of the workpiece is very low, the general temperature does not exceed 100℃, which is the most prominent advantage compared with other thermal cutting processes. This eliminates the possibility of deformation of the cutting part, the heat-affected zone of the cutting part, and the possibility of tissue change. It can be used safely and reliably in places where fireworks are strictly prohibited, such as offshore oil drilling platforms, oil refineries, large oil tanks and oil and gas pipelines.
(2) the cutting quality of water jet cutting is very good, the cutting surface is smooth, no burr and oxidation residue, the cutting gap is very narrow, with pure water cutting, generally can be controlled within 0.1 mm; Add a certain cutting abrasive between 1.2-2.0mm, the incision does not need secondary processing, simplify the processing procedure.
(3) The cutting screen range is relatively wide. Water knife cutting thickness is wide, the maximum cutting thickness can be greater than 100mm. For special steel plates with thickness of 2.0mm, the cutting speed can reach 100cm/min. Although water jet cutting speed is slightly inferior to laser cutting, but in the cutting process does not produce a lot of cutting heat, so in practical application, water jet cutting has more advantages.
(4) Wide range of cutting objects. This cutting method is not only suitable for metal and non-metal cutting, but also for the processing of composite materials and thermal materials.
(5) Excellent operating environment water jet cutting process no radiation, no splashing particles, to avoid the phenomenon of dust flying, do not pollute the environment. Uniform grinding water jet cutting, abrasive dust and chips can also be directly washed away by the water flow, into the collector, to ensure the health of the operator, can be called green processing. Because of the advantages of water jet cutting, it has broad application prospects in aerospace, atomic energy, petroleum, chemical industry, underwater engineering and construction industries.
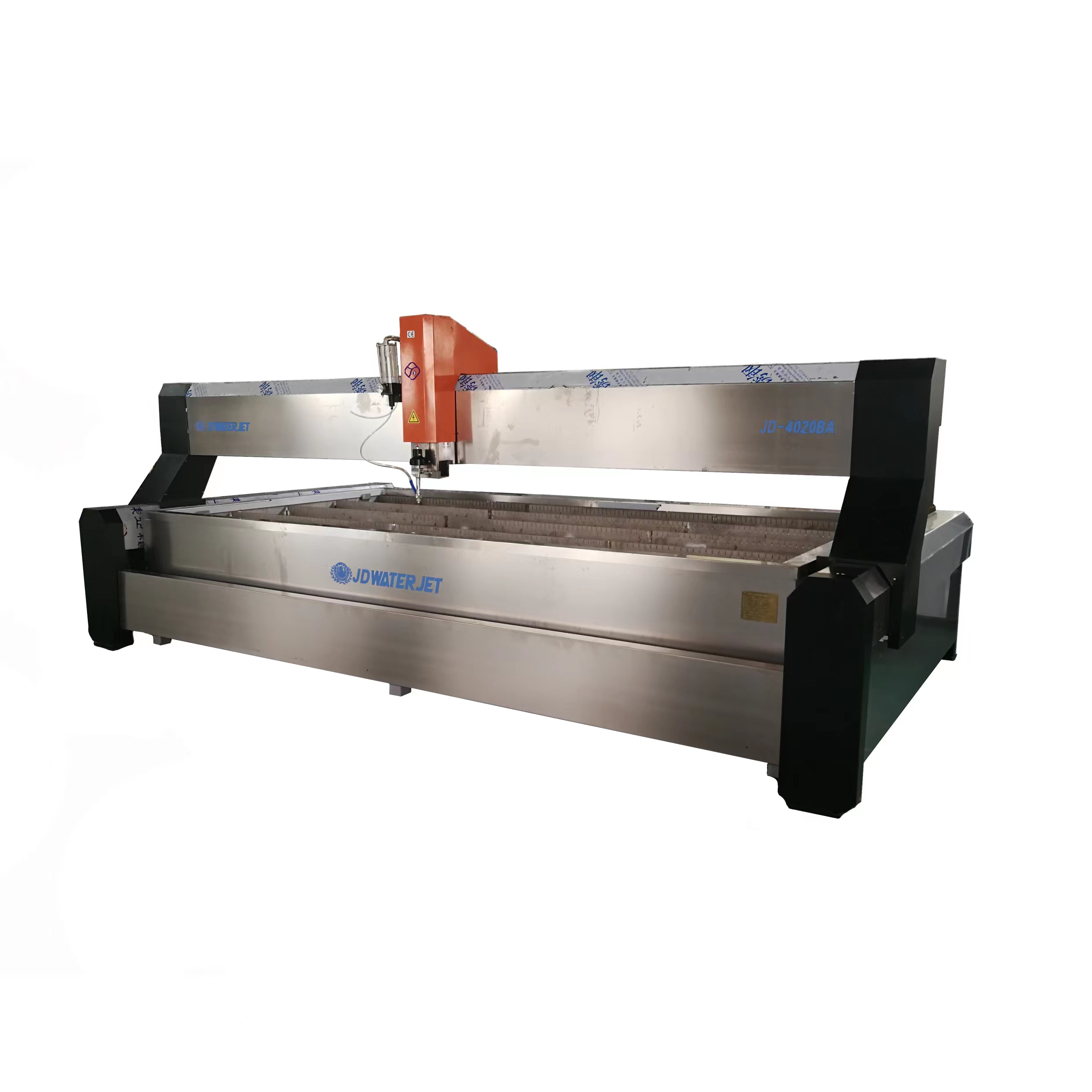
water jet cutting principle
Water jet cutting is a new cold machining technology. Can be used in bad conditions, prohibited fireworks, widely concerned. Water jet cutting is a combination of machinery, electronics and computers. The high-tech achievements of the whole automatic control technology is a new material processing method developed in recent years.
The principle of water jet cutting is to use a certain high pressure pure water or slurry with cutting abrasive, through the cutting nozzle injection liquid column with high density impact force, directly impact to be processed for cutting. According to the different water pressure, it can be divided into low pressure water jet cutting and high pressure water jet cutting.
water jet cutting characteristics
Water jet cutting technology has the following characteristics:
(1) Cutting water jet pressure is large. The pressure of the water jet is tens to hundreds of megapascals, which is 2 to 3 times the speed of sound, creating a huge energy density of the jet to cut objects. The cutting temperature of the workpiece is very low, the general temperature does not exceed 100℃, which is the most prominent advantage compared with other thermal cutting processes. This eliminates the possibility of deformation of the cutting part, the heat-affected zone of the cutting part, and the possibility of tissue change. It can be used safely and reliably in places where fireworks are strictly prohibited, such as offshore oil drilling platforms, oil refineries, large oil tanks and oil and gas pipelines.
(2) the cutting quality of water jet cutting is very good, the cutting surface is smooth, no burr and oxidation residue, the cutting gap is very narrow, with pure water cutting, generally can be controlled within 0.1 mm; Add a certain cutting abrasive between 1.2-2.0mm, the incision does not need secondary processing, simplify the processing procedure.
(3) The cutting screen range is relatively wide. Water knife cutting thickness is wide, the maximum cutting thickness can be greater than 100mm. For special steel plates with thickness of 2.0mm, the cutting speed can reach 100cm/min. Although water jet cutting speed is slightly inferior to laser cutting, but in the cutting process does not produce a lot of cutting heat, so in practical application, water jet cutting has more advantages.
(4) Wide range of cutting objects. This cutting method is not only suitable for metal and non-metal cutting, but also for the processing of composite materials and thermal materials.
(5) Excellent operating environment water jet cutting process no radiation, no splashing particles, to avoid the phenomenon of dust flying, do not pollute the environment. Uniform grinding water jet cutting, abrasive dust and chips can also be directly washed away by the water flow, into the collector, to ensure the health of the operator, can be called green processing. Because of the advantages of water jet cutting, it has broad application prospects in aerospace, atomic energy, petroleum, chemical industry, underwater engineering and construction industries.
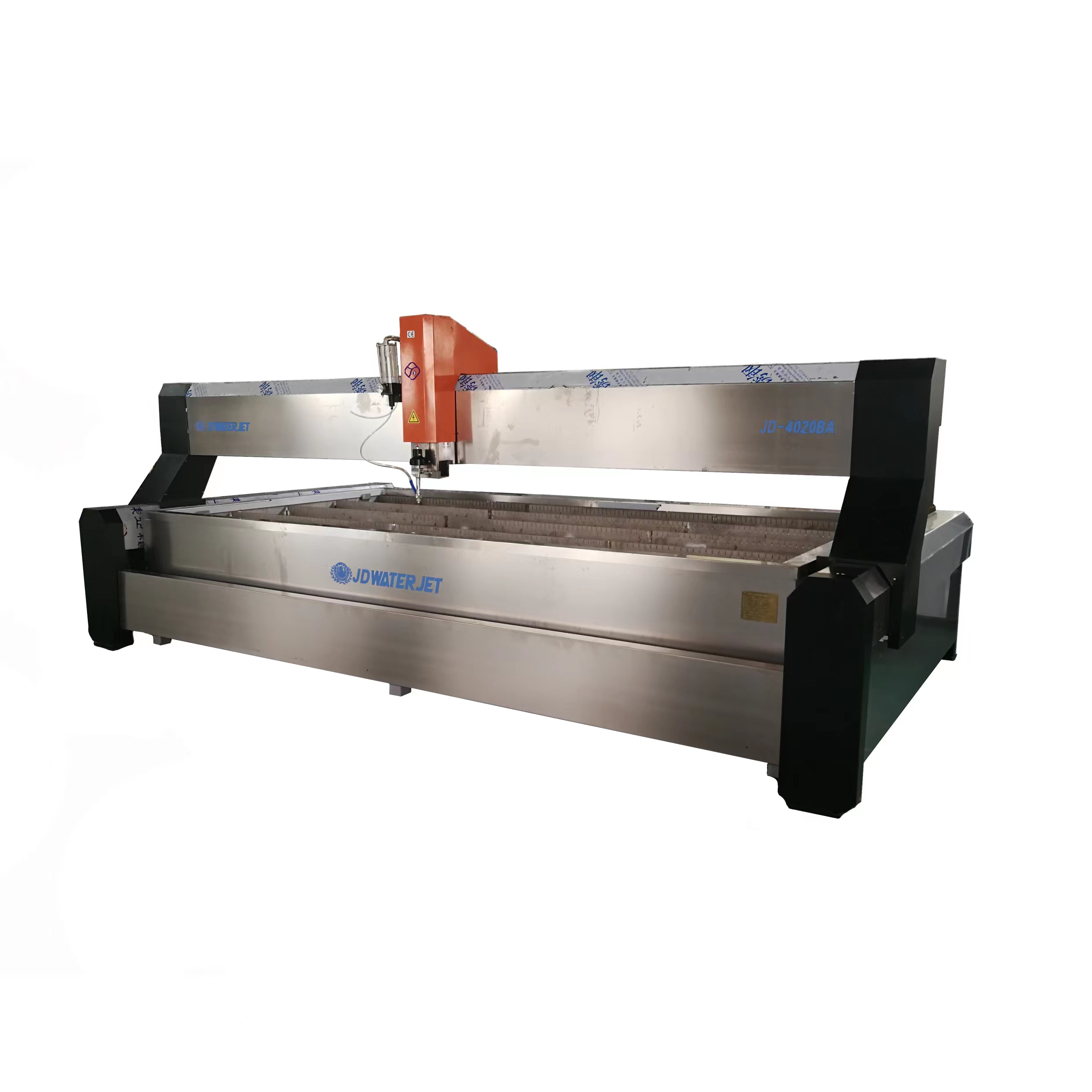
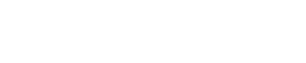
professional firm engaged in the research, development, sale, and service of Steel Shot, Steel Grit, sandblaster, sandblasting machine, garnet sand. We are located in Jinan with convenient transportation access. .
Quick links
Products Structure
Our Contacts
No.365 ,The Second Jing Road ,Huaiyin District, Jinan City ,Shandong Province ,China
0086-531-82020205
+0086-15806668333