News
How to select abrasives in low carbon era
17/7/2025
Selecting the right abrasive for surface blasting depends on the material being blasted, the desired finish, and environmental considerations. Key factors include hardness, density, shape, and size of the abrasive, as well as the abrasive's ability to create the desired surface profile. Environmental and cost factors also play a crucial role in the selection process. Factors to Consider When Choosing Abrasives:
I Material:
Hardness: Harder abrasives like aluminum oxide and silicon carbide are suitable for removing tough coatings and creating a deep anchor profile. Softer abrasives like glass beads are used for delicate cleaning and surface finishing.
Density: Denser abrasives like garnet deliver more impact energy, creating a deeper profile and removing material more effectively.
Shape: Angular abrasives cut deeper and create a rougher surface profile, while rounded abrasives provide a smoother finish.
Size: The ideal particle size depends on the thickness of the material being removed. Larger particles can remove thicker coatings but may reduce the "hit rate" and require more abrasive. Smaller particles provide better coverage and faster cleaning, but may not be suitable for heavy-duty applications.
Surface Finish:
Consider the desired surface profile for subsequent coating or painting. Angular abrasives are ideal for creating a rough surface for better coating adhesion.
Environmental Concerns:
Dust Generation: Some abrasives, like sand, generate more dust than others, which can impact worker safety and environmental regulations.
Recyclability: Tough abrasives like garnet can be recycled, reducing material costs and waste.
Cost: Consider the initial cost of the abrasive and its efficiency in terms of material usage and blasting time.
Ii Types of Abrasives:
Metallic Abrasives:
Steel Grit/Shot: Durable and aggressive, suitable for heavy-duty cleaning and surface preparation.
Stainless Steel Grit/Shot: Non-contaminating, suitable for applications where rust or corrosion is a concern.
Mineral Abrasives:
Garnet: A natural abrasive, known for its hardness, density, and ability to create a good anchor profile.
Aluminum Oxide: Durable and effective for removing tough coatings and preparing surfaces.
Glass Beads: Provide a smoother, less aggressive finish, suitable for delicate cleaning and peening.
Silicon Carbide: Extremely hard and aggressive, ideal for etching hard metals and creating a deep profile.
General Recommendations:
Start with the smallest abrasive particle size that effectively removes the material and achieves the desired profile.
Choose a tougher abrasive for applications requiring multiple uses and recyclability.
Consider the environmental impact of the abrasive and its disposal.
Consult with abrasive suppliers for specific recommendations based on your application and material requirements.
By carefully considering these factors, you can choose the right abrasive for your surface blasting needs, ensuring optimal performance, desired finish, and environmental compliance.
Any further details you need, please feel free to contact.
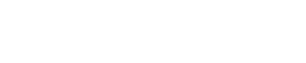
professional firm engaged in the research, development, sale, and service of Steel Shot, Steel Grit, sandblaster, sandblasting machine, garnet sand. We are located in Jinan with convenient transportation access. .
Quick links
Products Structure
Our Contacts
No.365 ,The Second Jing Road ,Huaiyin District, Jinan City ,Shandong Province ,China
0086-531-82020205
+0086-15806668333