News
Advantages and disadvantages of waterjet cutting ,Vs Laser Cutting
24/9/2022
Water jet cutting ( waterjet) is a type of computer controlled cold cutting (CNC) that allows cutting large thicknesses, with great precision and in a wide variety of materials.
The working principle of water jet cutting is that water is pressurized to approximately 400 MPa and then forced out of a nozzle at speeds of up to 900 m/s. Depending on the type of material to be cut, it can be cut only with water (soft materials) or by mixing the water with abrasive particles (hard materials, for example steel, stainless steel, etc.)
The joint action of water plus abrasive allows cutting a very wide variety of materials: metals, stones, ceramics, glass, composite materials, plastics, rubber, leather, etc. Cutting thicknesses can be up to 200mm depending on the material. The cutting groove typically varies between 1.5 and 2mm ,depending on the type of material.
the advantages of the waterjet cutting are:
1.Much greater thicknesses can be cut, in the case of steel, water cutting can reach up to 100mm.
2.All types of materials can be cut regardless of physical properties such as diffusivity or reflectivity. Difficult materials to cut by laser such as copper, bronze, aluminum, and others can be cut with water without much difficulty.
3.As it is a cold cut, it does not produce any alteration to the physical properties of the material.
4.No burrs (contrary to thermal processes).
5. Much smaller details can be cut than with laser cutting.
We can highlight as an advantage that it has the ability to cut tubes and profiles, angled cut and cut composite materials thanks to a drilling head.
The main disadvantages of water jet cutting, compared to laser cutting are:
1. The width of the cutting groove is much greater.
2. In the range of thicknesses and materials where laser cutting is used, cutting speeds are much higher than those of water cutting.
3. From the previous point it also follows that the costs of water cutting are much higher than those of laser cutting (in materials and thicknesses that can be laser cut).
4. It is a noisy cutting procedure
Finally, we can conclude that water jet cutting is a non-thermal process that allows cutting large thicknesses and a wide range of materials with great detail capacity, but at lower speeds and higher costs than laser cutting.
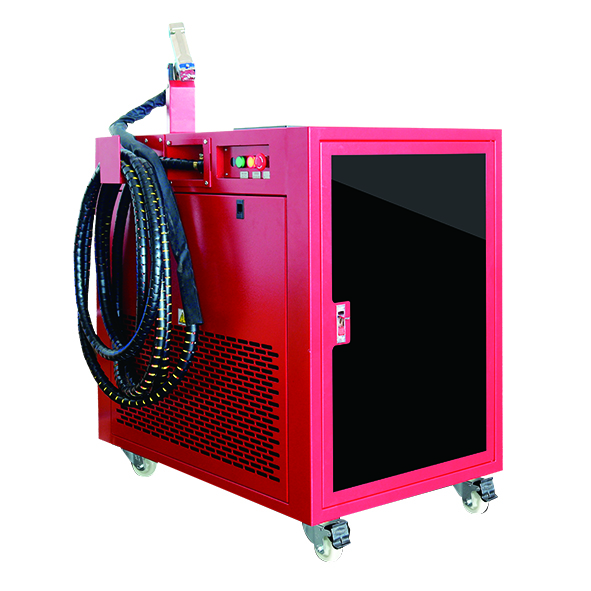
The working principle of water jet cutting is that water is pressurized to approximately 400 MPa and then forced out of a nozzle at speeds of up to 900 m/s. Depending on the type of material to be cut, it can be cut only with water (soft materials) or by mixing the water with abrasive particles (hard materials, for example steel, stainless steel, etc.)
The joint action of water plus abrasive allows cutting a very wide variety of materials: metals, stones, ceramics, glass, composite materials, plastics, rubber, leather, etc. Cutting thicknesses can be up to 200mm depending on the material. The cutting groove typically varies between 1.5 and 2mm ,depending on the type of material.
the advantages of the waterjet cutting are:
1.Much greater thicknesses can be cut, in the case of steel, water cutting can reach up to 100mm.
2.All types of materials can be cut regardless of physical properties such as diffusivity or reflectivity. Difficult materials to cut by laser such as copper, bronze, aluminum, and others can be cut with water without much difficulty.
3.As it is a cold cut, it does not produce any alteration to the physical properties of the material.
4.No burrs (contrary to thermal processes).
5. Much smaller details can be cut than with laser cutting.
We can highlight as an advantage that it has the ability to cut tubes and profiles, angled cut and cut composite materials thanks to a drilling head.
The main disadvantages of water jet cutting, compared to laser cutting are:
1. The width of the cutting groove is much greater.
2. In the range of thicknesses and materials where laser cutting is used, cutting speeds are much higher than those of water cutting.
3. From the previous point it also follows that the costs of water cutting are much higher than those of laser cutting (in materials and thicknesses that can be laser cut).
4. It is a noisy cutting procedure
Finally, we can conclude that water jet cutting is a non-thermal process that allows cutting large thicknesses and a wide range of materials with great detail capacity, but at lower speeds and higher costs than laser cutting.
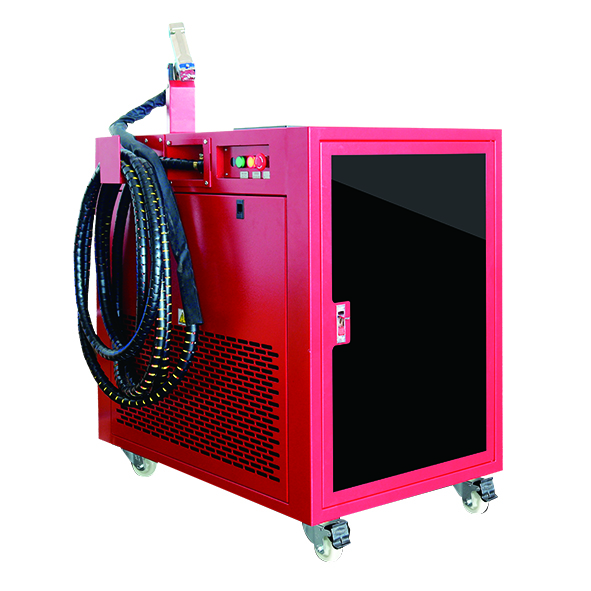
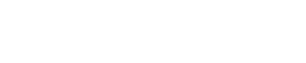
professional firm engaged in the research, development, sale, and service of Steel Shot, Steel Grit, sandblaster, sandblasting machine, garnet sand. We are located in Jinan with convenient transportation access. .
Quick links
Products Structure
Our Contacts
No.365 ,The Second Jing Road ,Huaiyin District, Jinan City ,Shandong Province ,China
0086-531-82020205
+0086-15806668333
-
Message